Sprint 2
Weeks 3-4
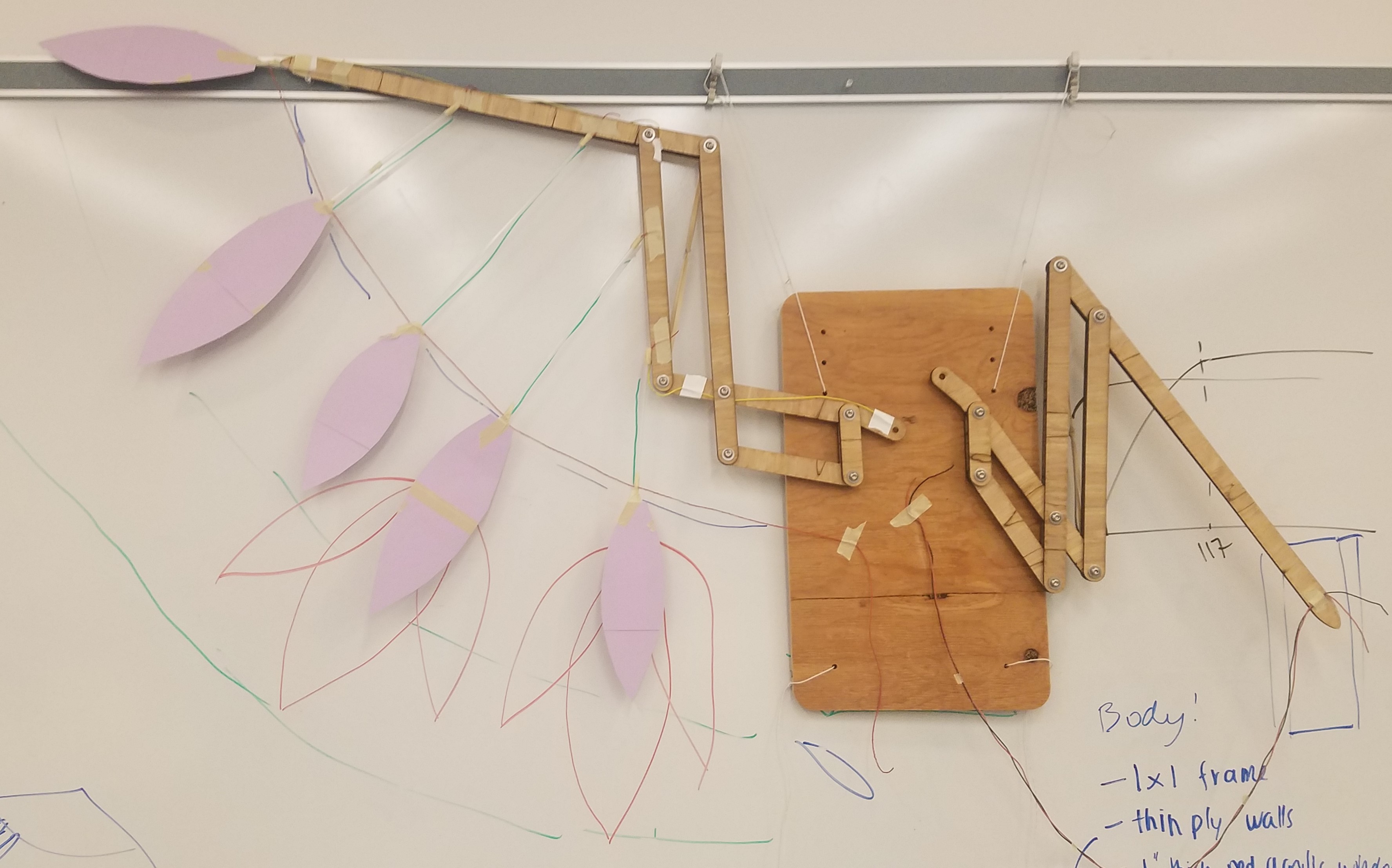
Sprint Overview
For this sprint we refined our linkage design, made a full scale model of our linkage system, and started to mock up feather placement and design. We started prototyping a harness design that could be modified to fit the specific user. On top of that, we experimented with using force sensors to control the movement of the wings and planned how these would integrate into our system.
Linkages
We determined full scale linkage dimensions and laser cut and assembled them out of plywood.
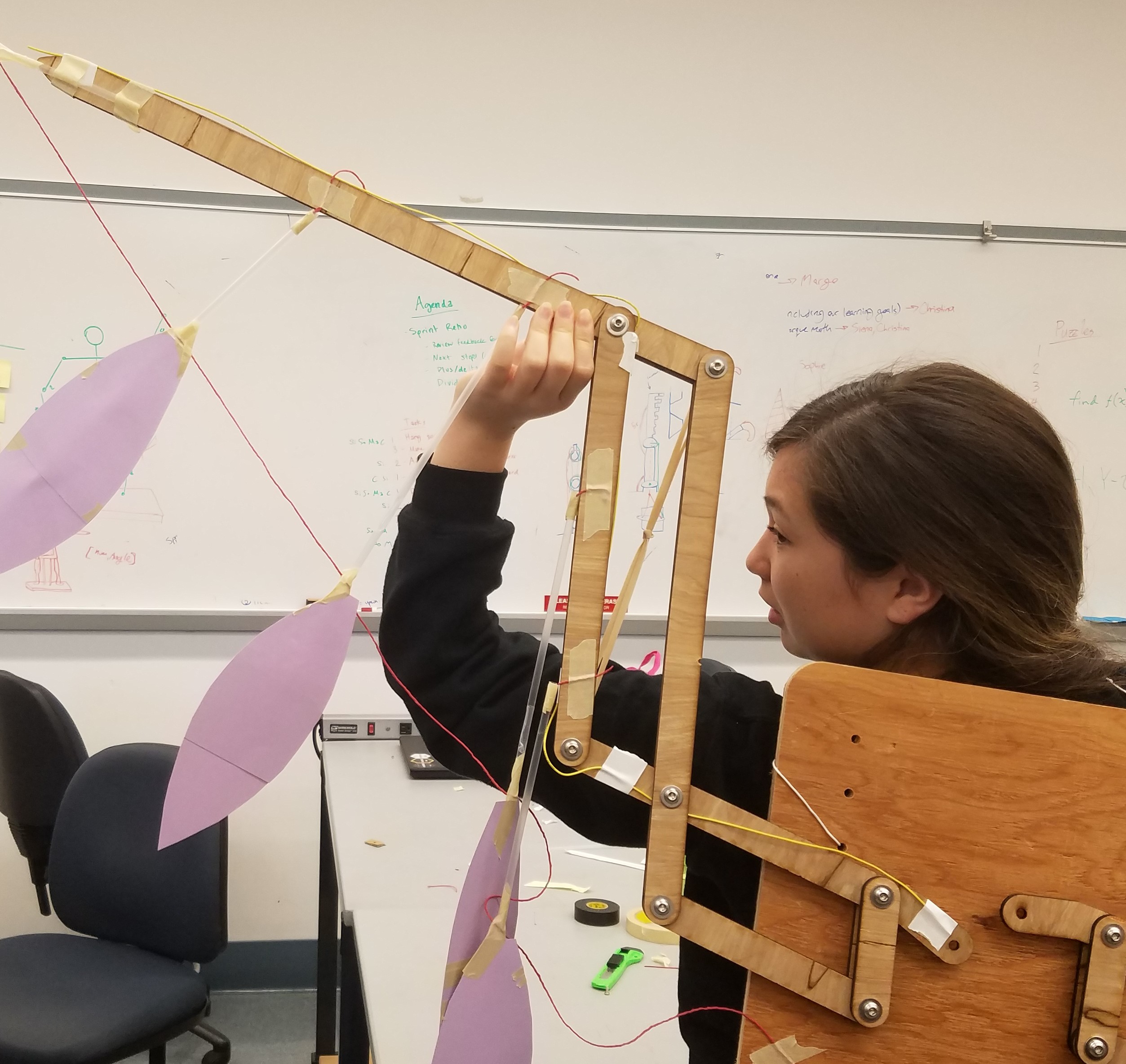
Actuation
We ran careful calculations in order to spec out appropriate motors for our application. We wanted to make sure the motors had enough torque to lift the wing assembly, but not too much power that they would put unnecessary strain on other components. This involved first calculating the torque needed to lift a wing by accurately estimating the weight through materials modeled in CAD.
We included a large factor of safety in our calculations so that we knew the motors would be able to lift the load we put on it. This also included gearing down the motors that already had build-in gearboxes.
We then compared price, weight, and stall torque of different motors available. Looking at data sheets such as a motor data curve (shown below), we picked out a pair of motors that met our requirements.
Harness
In order to design a harness that was both comfortable and adjustable, we took inspiration from hiking backpacks. Hiking backpacks are made to distribute most of the weight being carried over the wearer's hips. They also have a rigid back frame that allows the weight to remain evenly apportioned and not all in one spot. We integrated these findings into our own harness design, with padded shoulder and hip belts. Our first model was made of cardboard and included a live hinge for better fitting towards the curves of the wearer's back. We then found that we needed a sturdy backboard to attach all the components securely, so we opted for a harder plywood version.
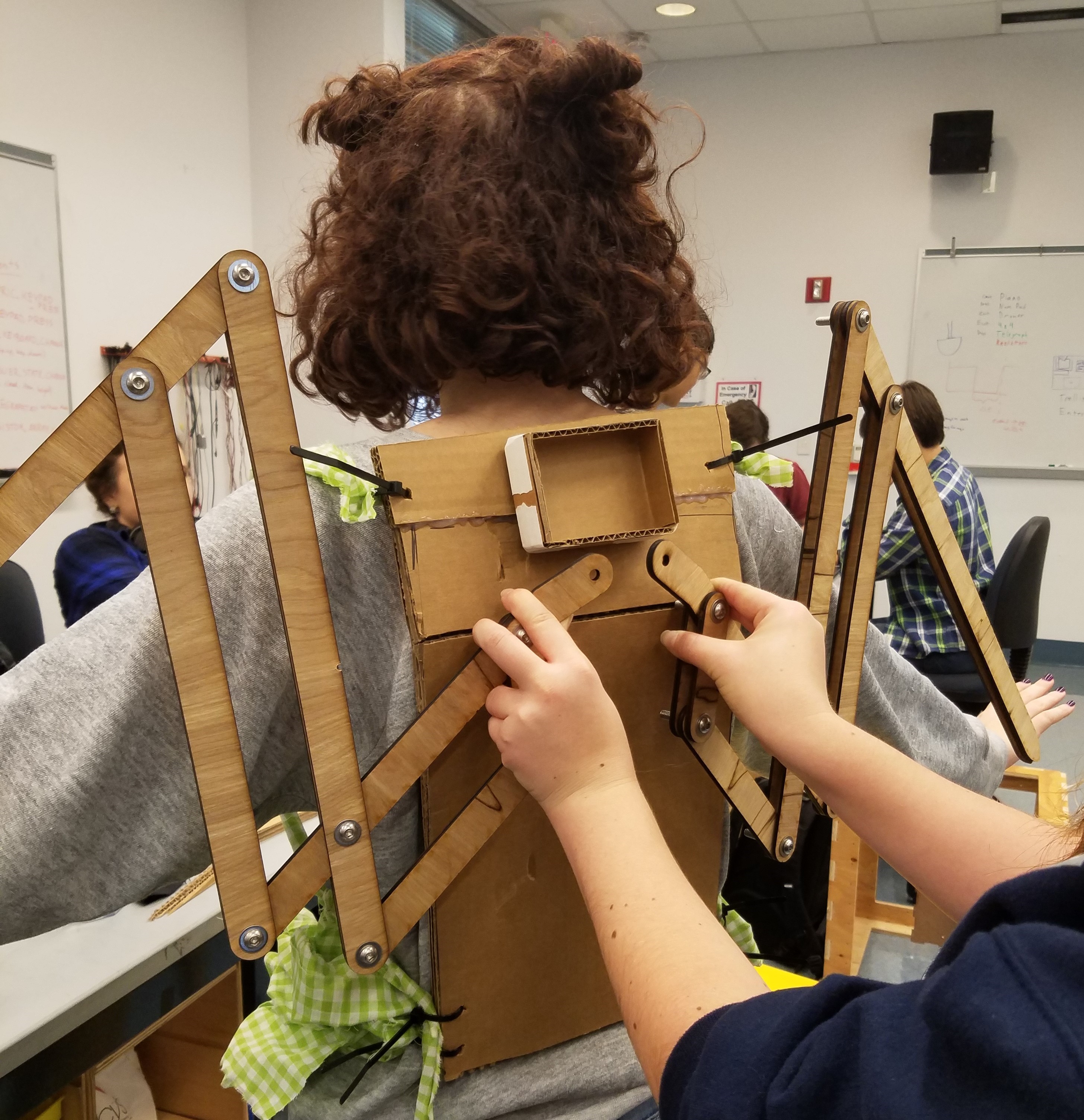
Feathers
In this sprint we had an all-team meeting to come up with a cohesive plan for what we wanted our aesthetic to be. We decided on a "dark angel" look that included long black feathers with dark blue accents. We created models of some of these with wire and zip tie spines to get rough weight approximations for calculation purposes.
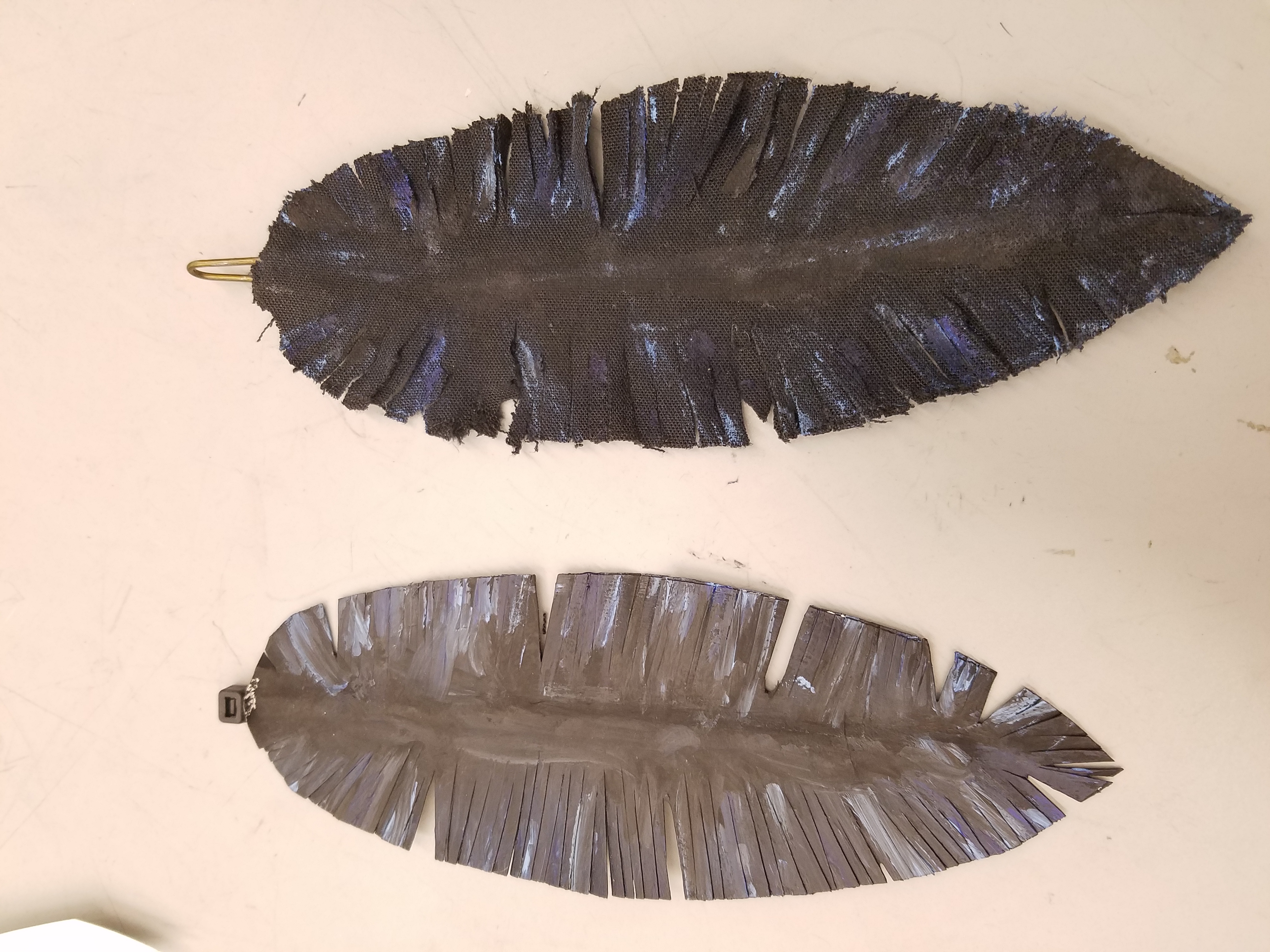
Running Wires
We decided on wiring the distance sensors in a structural way, by attaching them to the feathers. This both removed the worry of running wires along the linkage, and created a way to space the feathers out for aesthetic purposes.
Added Fluttering Motion
We used our small wing prototype to test some more complicated motion. One of these motions was fluttering, where on the way up and down, the wings bounce slightly.
Force Cuff
To incorporate arm movement with our wing position, we used a force sensor, which, when placed on an arm and attached with elastic, increases in value with an increase in arm angle. We prototyped it with a fabric and rubber band arm harness, and were able to move the wing in response to the wearer’s arm position.
Problems Identified
We need method of attaching different parts together (harness, strain gauges, wings).
Motor purchasing has been held up by weight estimates, but we will order that in the coming days.
Harness needs to incorporate adjustability for different back sizes.