Calibration and Safety
What keeps everything from breaking.
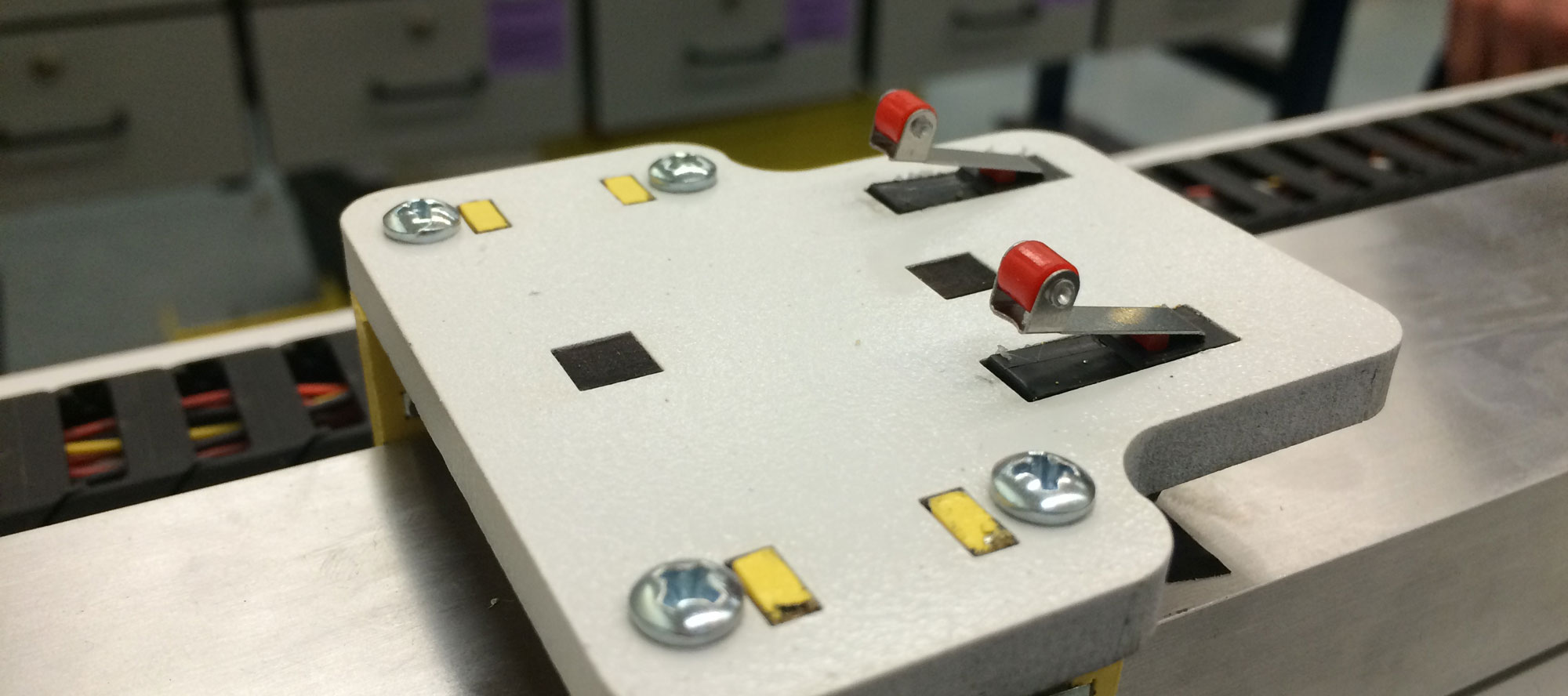
Eight limit switches provide physical feedback for the gantry. Four of these enable the gantry to know “where” it is when it turns on for the first time. When running its homing operation, which happens on startup, the gantry moves in all possible directions (one direction at a time) until it hits a calibration limit switch, then moves to home (the established bottom left location) and remembers the maximum distance it can go in either direction.
Four additional limit switches trigger an emergency stop to all high-powered electronics (the stepper motors, air pump, and solenoid) except for the griddle. These limit switches are located a quarter of an inch past the calibration limit switches in every direction. In the event that calibration fails or the steppers begin receiving power from an alternate source, hitting the limit switches will immediately cut power, not only to the motor but also to the extrusion components. Since the solenoid is normally-closed, the machine will halt extrusion when this emergency stop is triggered.
Even in the case that emergency stop limit switches don’t get triggered (for example, if the limit switches break and stay open) no harm can be caused. When the gantry makes physical contact with the guide rod support boxes, the stepper motors will deform the 3D-printed pulley. This ensures that neither the stepper motor nor any component of the gantry will get damaged.