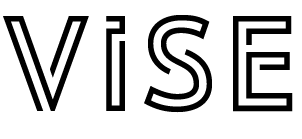
The vise secures the foam piece onto the plate while the piece is revolving and being cut by the hot wire.
.jpg)
Secure rotation
In order to ensure that the vise doesn’t shake while rotating, we fabricated a bearing block from aluminum stock so that the plate axle would go through. The block had a bearing race track where the bearing balls can sit. The plate support sits on top of the bearing balls and the balls prevent the plate support from wobbling.
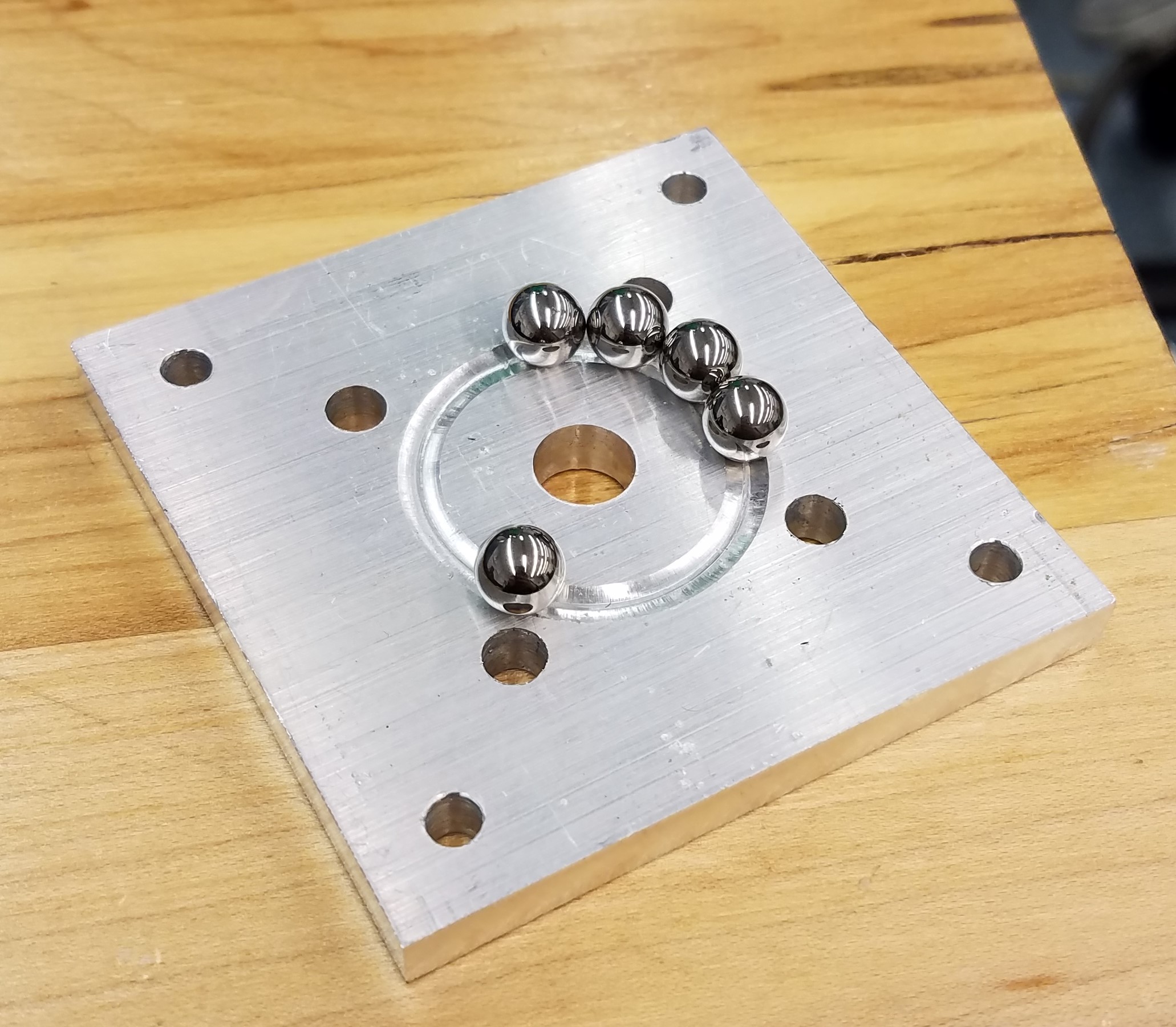
Easy Plate Interface & Block Secure
On the center of the plate there are two wooden spikes that the styrofoam block can penetrate. Users can easily position the styrofoam block onto the plate without worrying about the block shaking.
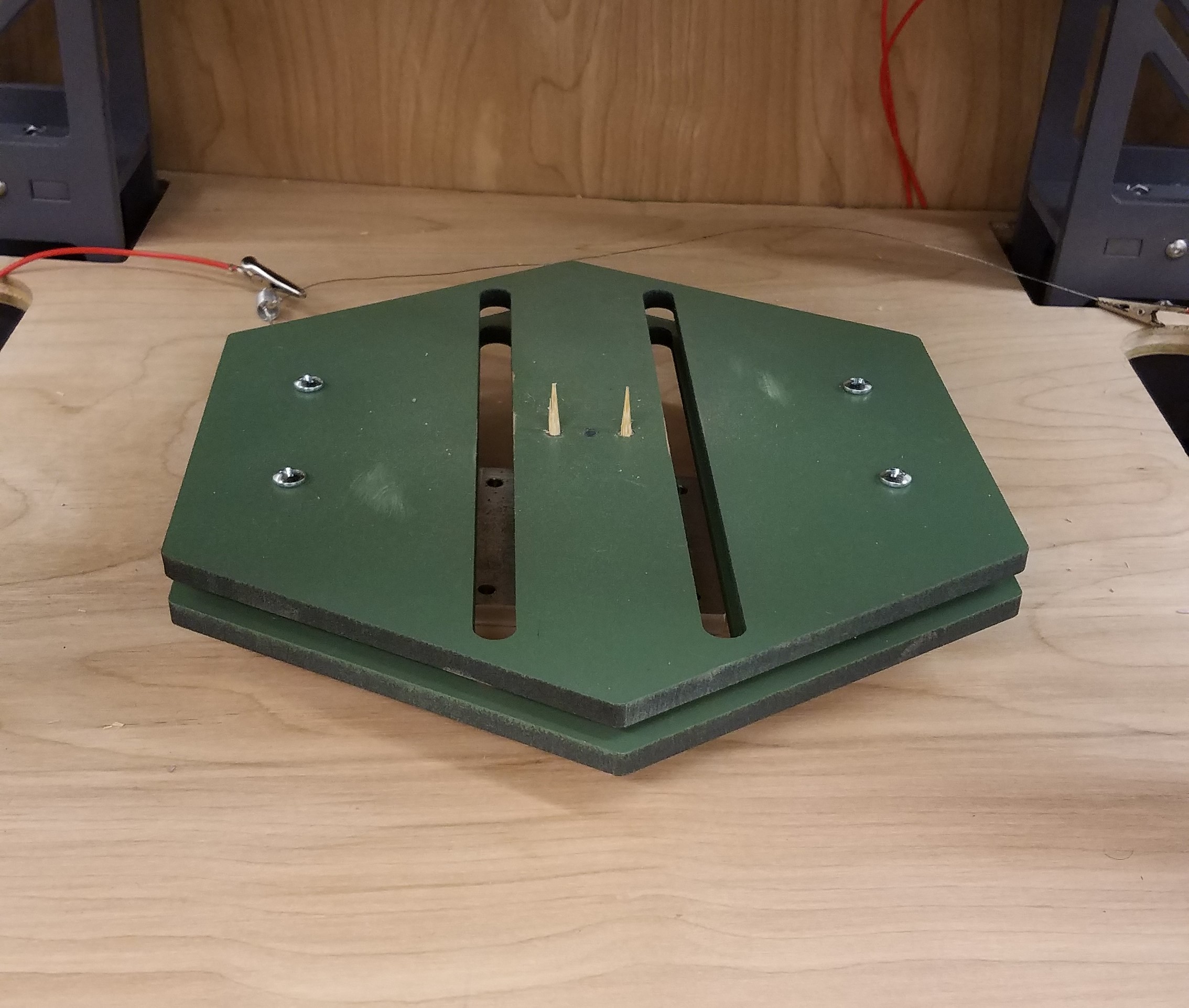
Sprint 1
For sprint 1 we didn’t have a great way to secure the piece. We first taped the piece to the table and then because the tape kept lifting, we simply squeezed the styrofoam block between two wood blocks and hoped that the piece wouldn’t move. We realized that the wood blocks didn’t fully constrain the foam blocks and the wire would catch on the foam and start rotating it, so we knew we would have to figure out a better way of holding the piece.
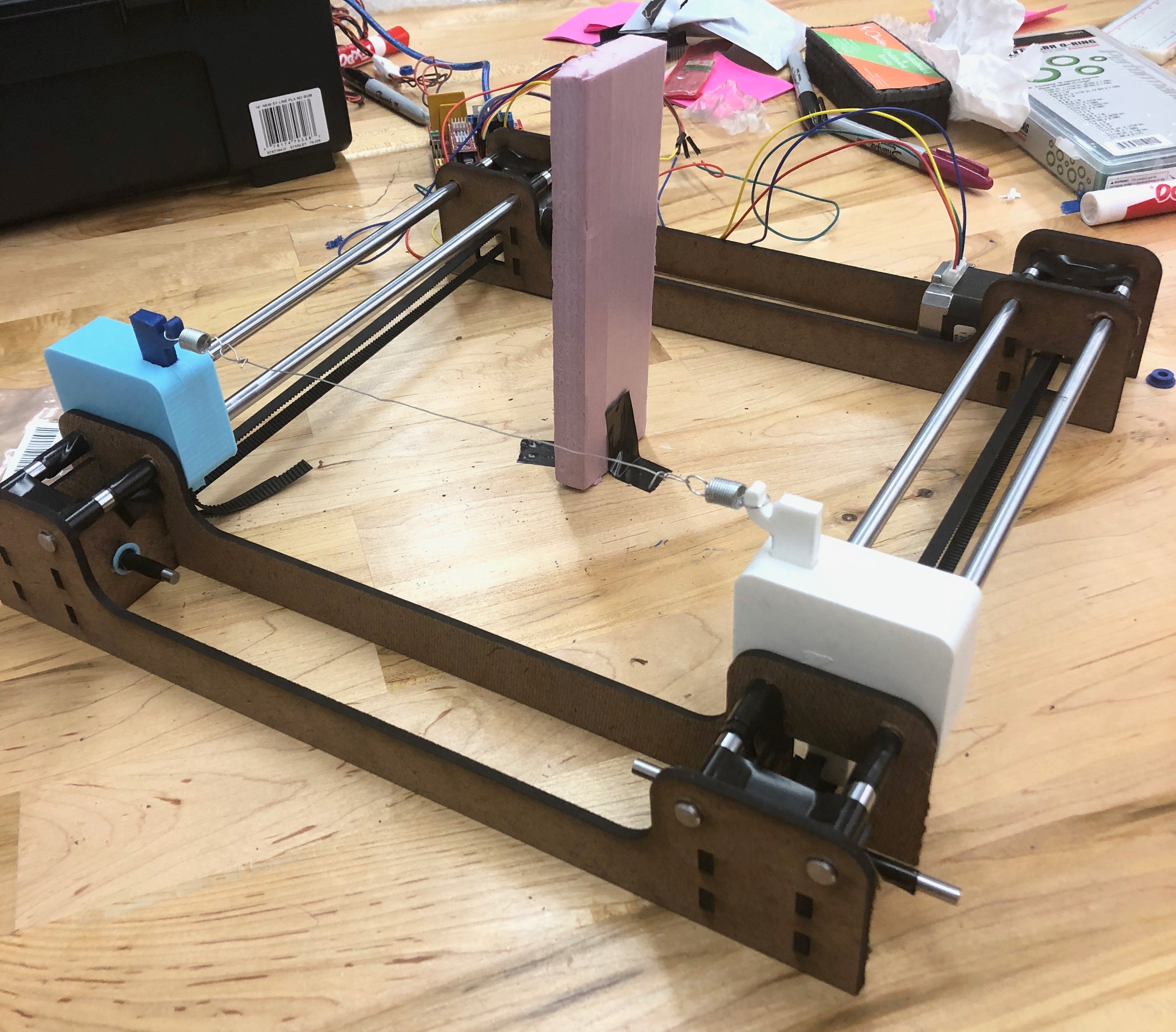
Sprint 2
For sprint 2 we designed a preliminary vise, where we had two 3D-printed grips that slid across the rail printed on the vise plate. Though this was somewhat effective in keeping the piece, it was challenging to hold the piece and secure the position of grips at the same time. We would successfully secure the position of the grips, but it wouldn’t fully grab the styrofoam piece. Furthermore, the axle that rotated the vise plate wobbled, which made the overall position of the piece unstable. Therefore, we concluded that there should be an easier way to secure the styrofoam block and a method to keep the plate axle from wobbling.
Sprint 3
For sprint 3 we CADed the final vise, where we had a bearing plate with a circular race of bearing balls that the plate could sit on and still rotate while preventing wobble and a 10” two-sided lead screw that simultaneously moved the 3D-printed grips and effectively secured the piece. Though we solved the instability issue of the plate, we realized that it was somewhat unnecessary to manufacture 10” two-sided lead screw. The plate rotated at around 1 revolution per second, so we realized that though the securing method was necessary to hold the piece, it didn’t necessarily need 10” lead screw that would very tightly grab onto the styrofoam block. We decided to scrap the lead screw idea and come up with an alternative, simple solution to securing the piece.
Final Product
For our final vise, we manufactured most of our CADed parts for our vise, but instead of using 10” double-sided lead screws, we decided to use wooden skewers to hold the foam piece. The skewers not only held the foam well but also were easily repairable in case they broke off. Once the securing method was finalized, the final vise was assembled and installed into our final product.
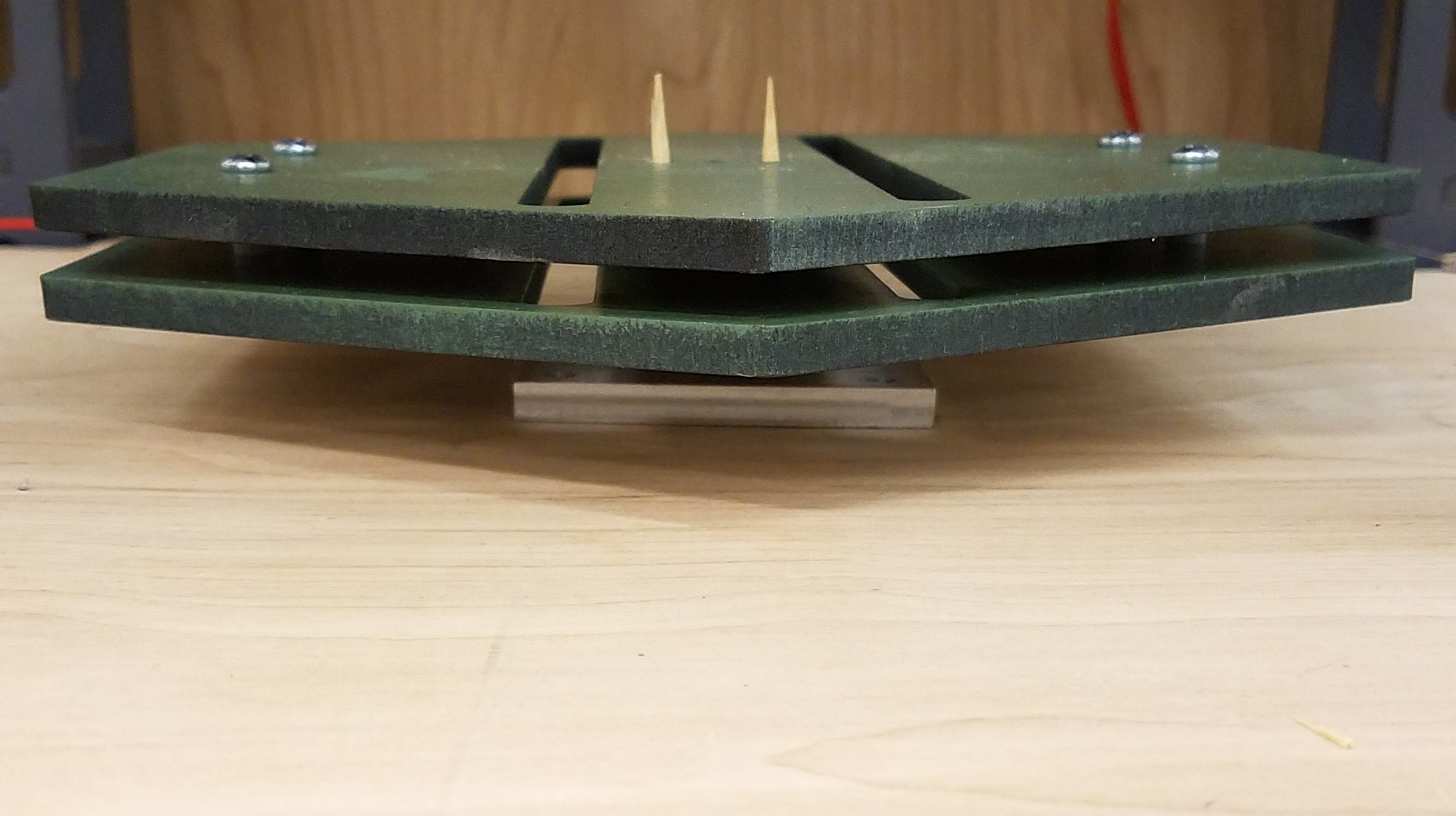