
Our enclosure serves as a way to house all of our components as one stand alone product, as well as ventilate the fumes created when cutting foam.

Front
Hidden from view, our power supply, arduino uno, and circuitry live in the bottom section of our enclosure
Visible through a sheet of acrylic featuring our product name, you’ll find the slotted sheet of MDF that our frame sits on, along with our motor control system, and lighting.
The main section of our enclosure is where the actual cutting happens.
The top section features our filters and fan, with ventilation slots to blow the clean air out the top of the enclosure.

Side
Both sides feature vinyl windows to view the cutting area.
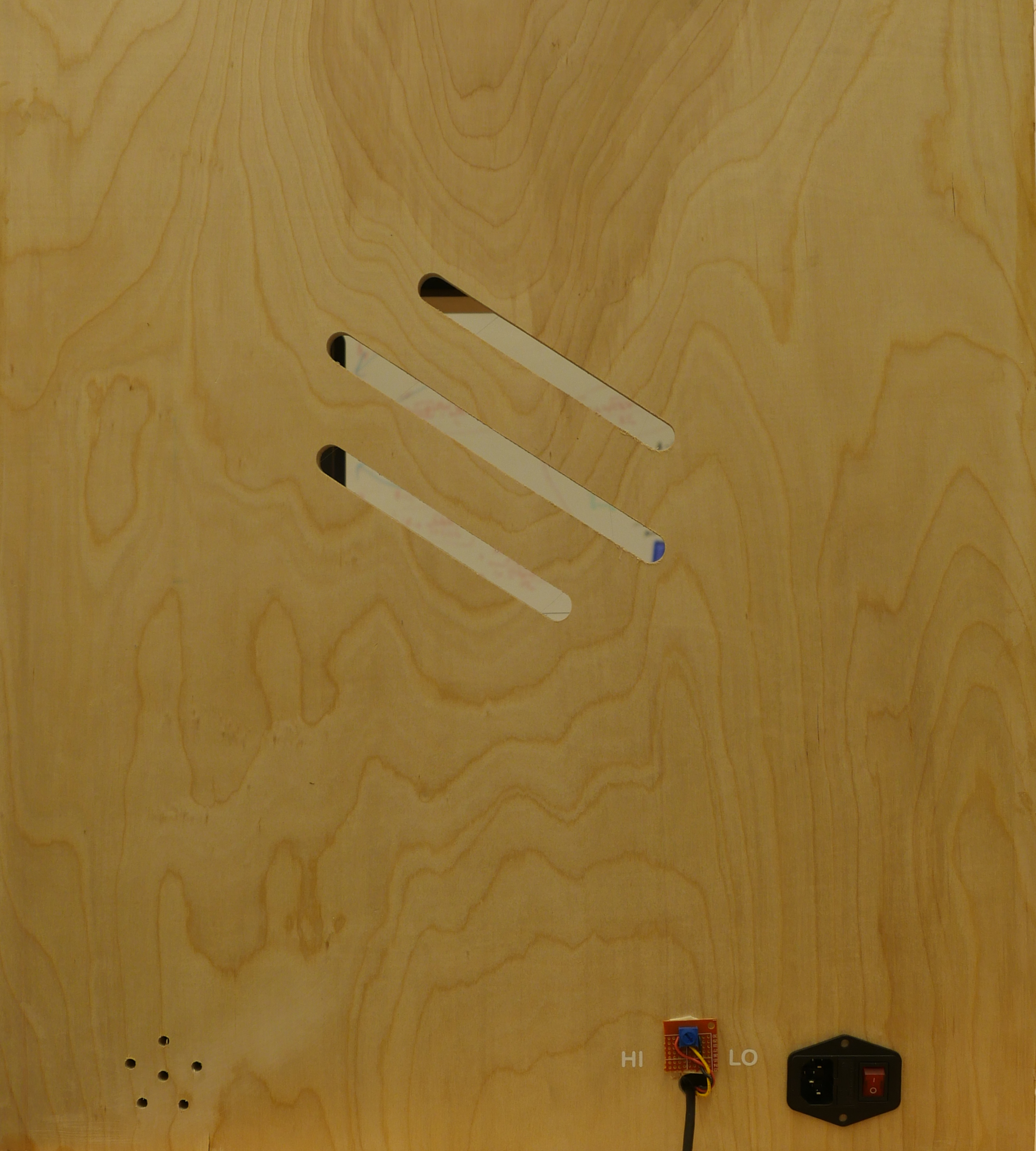
Back
The back of the enclosure has ventilation slots to pull air in through the cutting area, smaller ventilation holes for the power supply, a power socket with killswitch, and external control to the wire current.
Sprint 2 Enclosure
Our first enclosure was created for our Sprint 2 system. It was a simple 5 sided cardboard box with an open bottom and polycarbonate front that we could place over the top of our wire cutter. For ventilation, we wanted a system that wouldn’t take up a lot of space because our gantry was already so large. We decided not to use a shopvac because we didn’t need to clear out particles. After doing some air flow testing with fans and researching the ventilation systems used with we mounted fans to the top, and used a HEPA filter with carbon pre-filter to filter VOCs and particles.
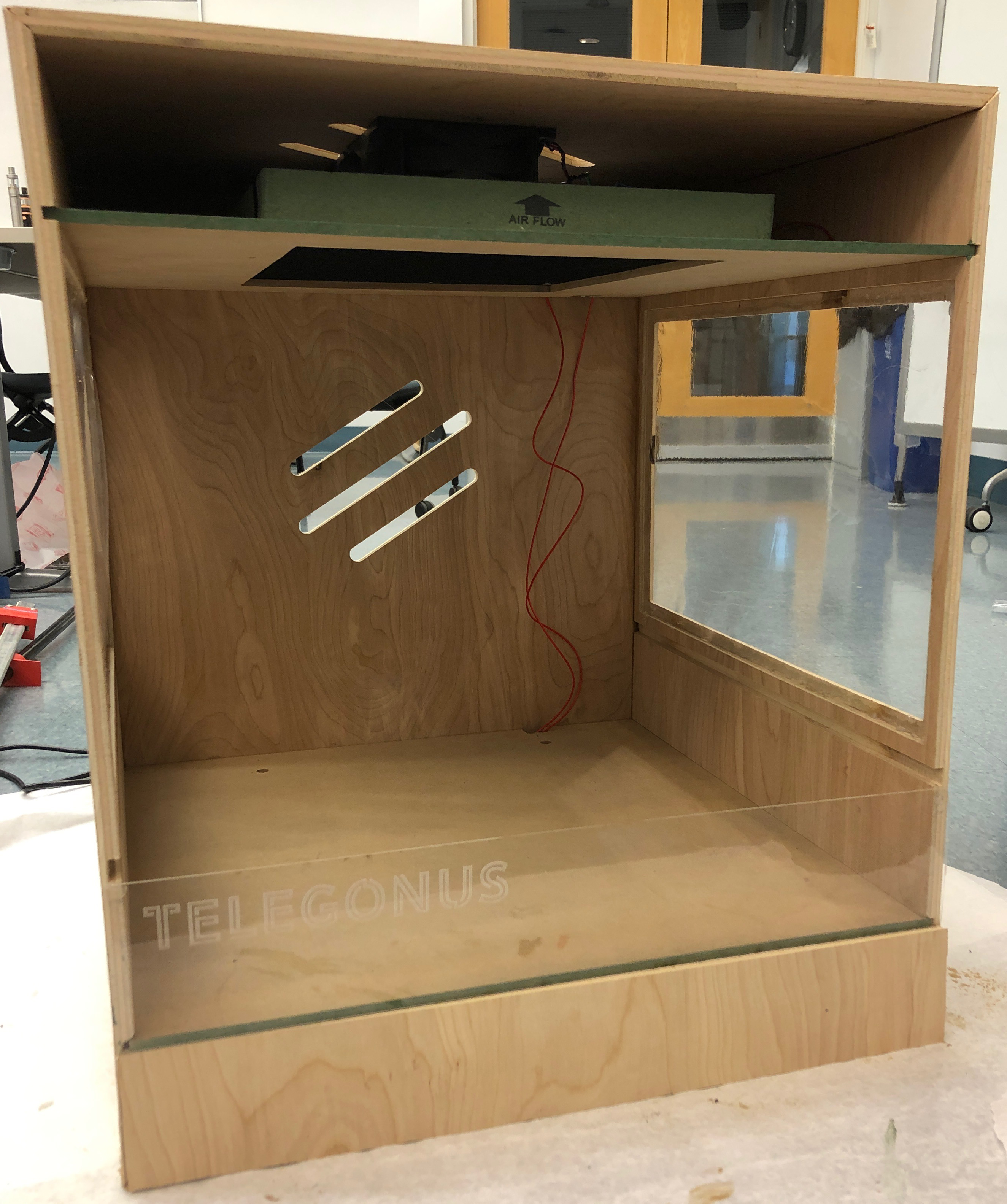
Final Enclosure
Our final enclosure is made from plywood, and machined on the Shopbot. Broken down into four sections, it separates our electrical components, base, cutting area, and filtration system. There are sheets of MDF that slot into the main structure that allows us to access the electrical components.