Mechanical Subsystem
The mechanical subsystem was composed of the turret’s frame, shooting mechanism, and hopper mechanism.
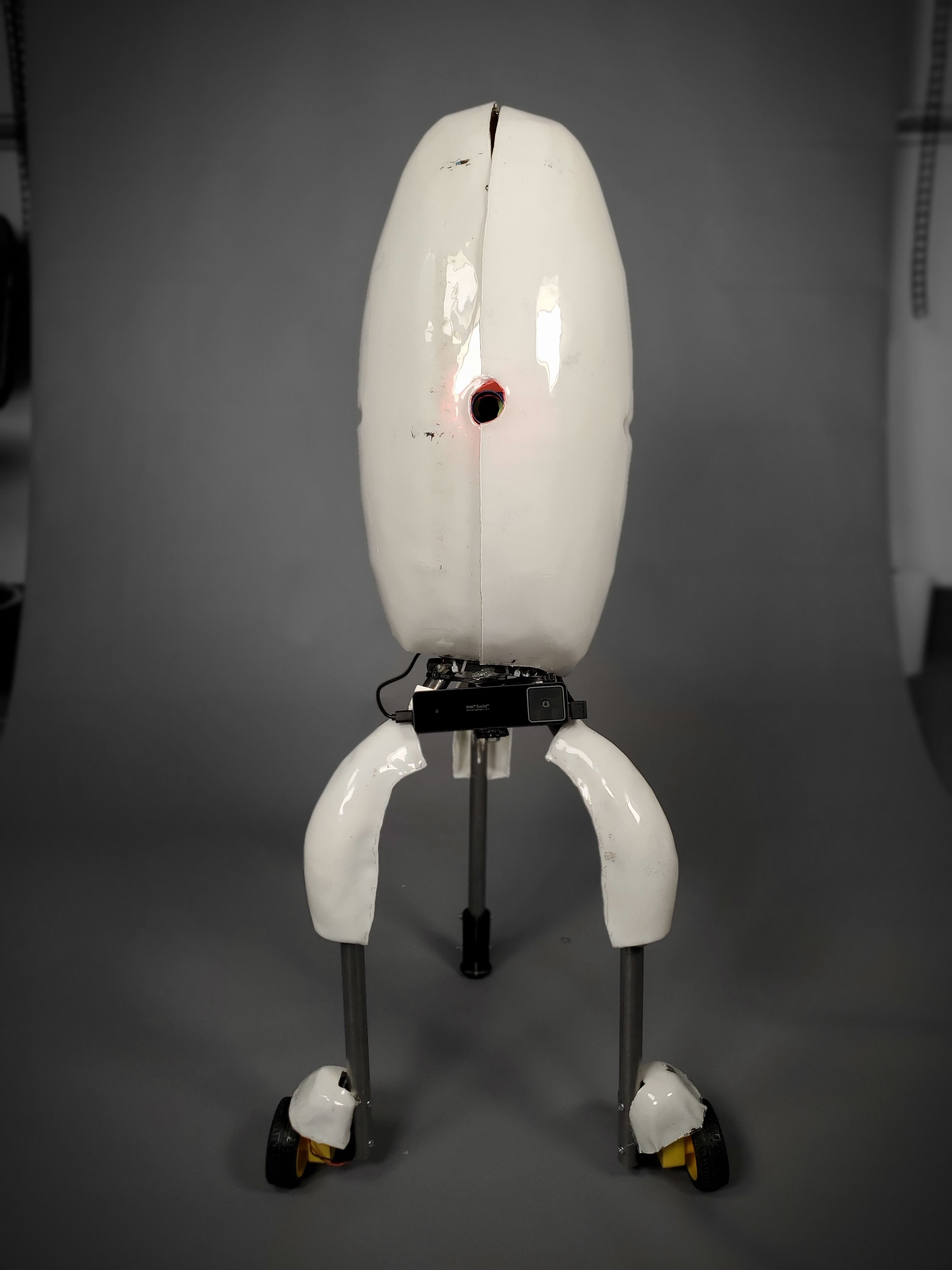
Turret Frame
The frame was designed in SOLIDWORKS to the specifications of a scaled 3D game file of the Portal Turret, utilizing an interlocking cross-sectional structure and baseplate. A pegboard was added to the central axis of the turrets frame for the purpose of later mounting and organizing the device’s internals. The frame was laser cut from hardboard and assembled with wood bonding glue in its press fit joints. The legs of the original frame were assembled and attached in a similar way, but were later upgraded to welded steel, mounted to the baseplate via an additional steel T-plate.
Shooter Block
The shooting mechanism was modeled after a dual flywheel launcher, and was comprised of a self-contained 3D printed brick with mounts for the wheels and motors. The mechanism positioned two drums spinning at high velocities on either side of a track for the foam ammunition, driven by 38,000 rpm motors, which could launch the projectiles at up to 50 mph.
Hopper
The shooting mechanism was fed by the hopper, a gravity fed ball storage mechanisms with a custom shaped lead screw mounted into the bottom. The lead screw pulled the foam projectiles from the bottom of the hopper and fed them into the spinning flywheels to fire a ball.
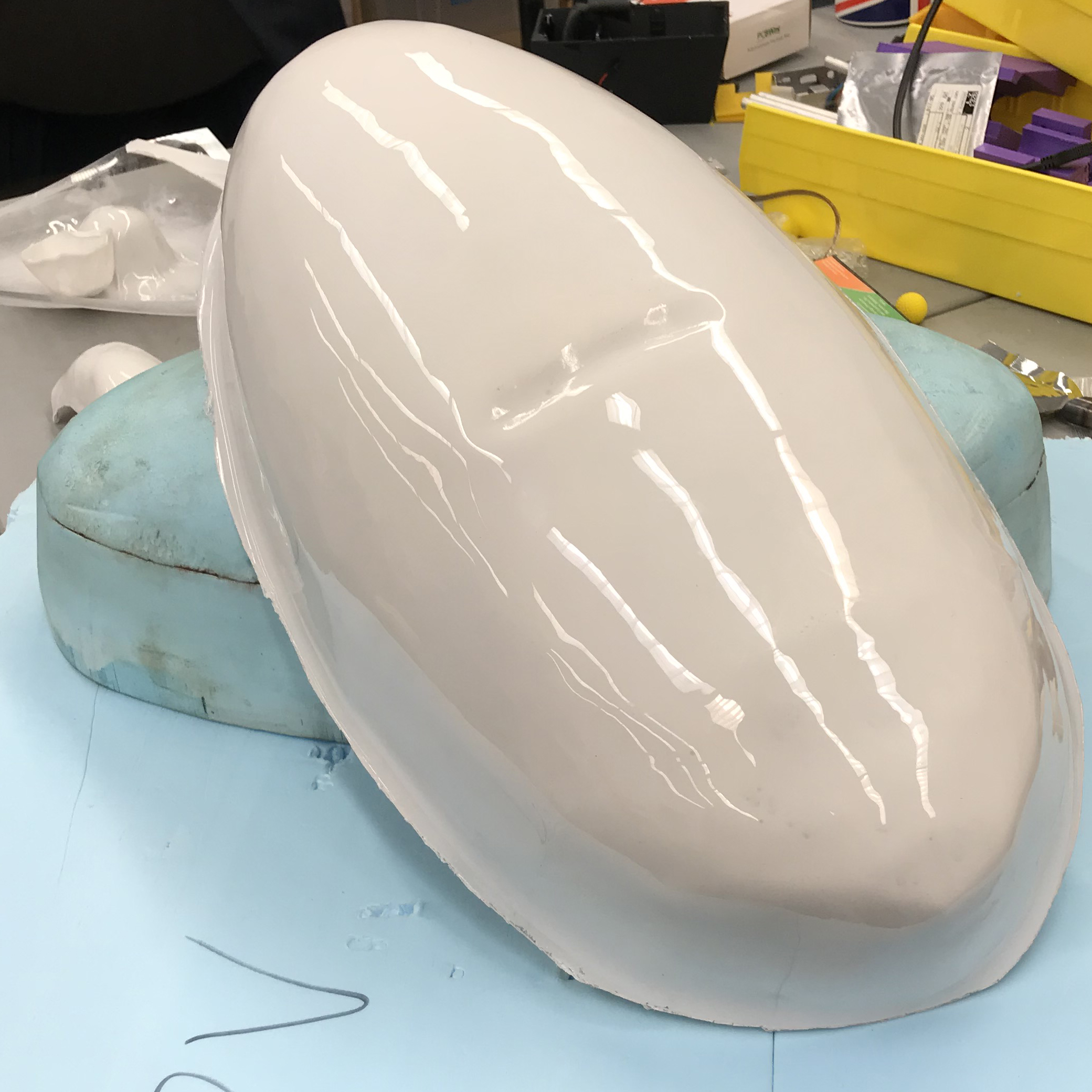
Shell
The finishing casing of the turret was made out of thermoformed plastic. To get the clean shiny aesthetic, the interior of the plastic was spray painted white. This let the clear plastic on the outside smooth the color and provide a glossy finish. The shell casings were then mounted to the turret magnetically to facilitate ease of removal to service the interior electronics.
Lessons learned in the process of construction
Shooter
The Shooter and firing mechanisms underwent many different iterations. Firstly the hopper had issues with balls jamming at first so it had be redesigned to keep the balls in seperate columns. Then the assembly tolerances were severly malformed and needed to be fixed. Then the screw would get stuck with soft balls because it would pull them through the sides instead of pushin them. Form this we learned to budget time for many iterations of each subsystem. Additionally make sure that your CAD components reflect the physical design of the parts, as an improperly sized cad for the continuous servo we had was the source of many of our tolerancing issues.
Firing mechanism
The firing mechnisms alsso went through several iterations. the first design did not leave enough motor shaft for proper adhesion of the wheels to the shafts. Then the motos were not clamped significantly enough to prevent walking during runtime vibrations. This involved redesiging the shooter to clamp at three seperate locations to the motors. The wheels orginally put the projectiles under too much strain which caused multiple problems of the motors boring through the wheels or the wheels stalling and melting. We redesigned the wheels to have a profile more akin to the shape of the projectiles this decreased the forces exerted on the wheels. From all this we reinforced the necessaty of multiple iterations of design, as well as the necessity of designing with the `on condition' in mind as the motors turning on vibrating and stripping out wheels caused many of the issues that we ran into.
Frame
We iterated several iterations of the frame. we started by building a rough box out of cardoard just to get a starting platform for the electrical team to build on. We whten wanted a more realistic representation of the robot shape so we designed a shaped frame made from lazer cut cardboar. This frame proved to be too small and flimsy as it collapsed under the weight of the electronics. This led us to laser cut hardboard to make a stronger iteration. The legs on this design proved to still be too flexible in the legs and so a final iteration of the legs was made where the legs were welded out of metal. The welds were not very clean and so we covered them with pieces of shell both to cover the weld beads, and to better represent tthe turrets form the portal games.