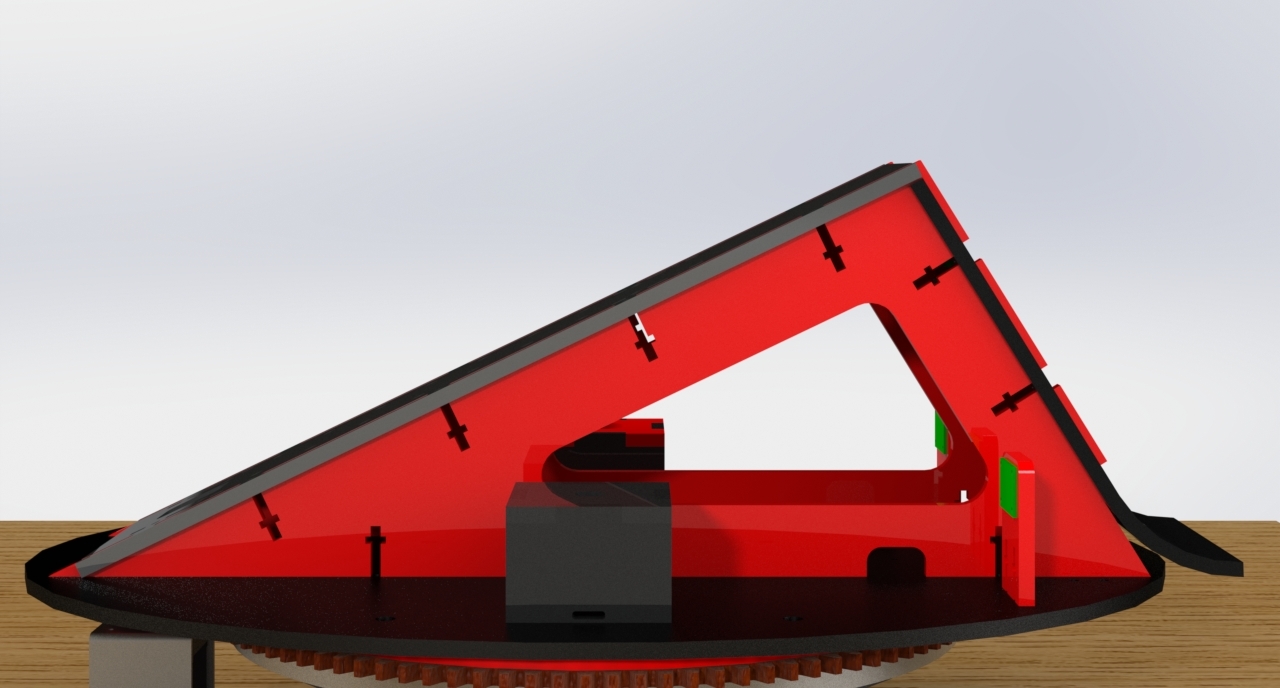
Description
On one side of the mountain structure triangle is the card advancer and on the other is the slide. The mountain structure is then secured onto the tabletop. Much like the rest of the structure it was made from 1/4" MDF that was lasercut in Olin's machine shop and fastened all together with our standard 8-32 screws and square nuts. The overall design of the card advancer has been through many modifications through four iterations, but it was key that modularity was always kept in mind. In our final iteration the lasercut parts were spray painted red and black.
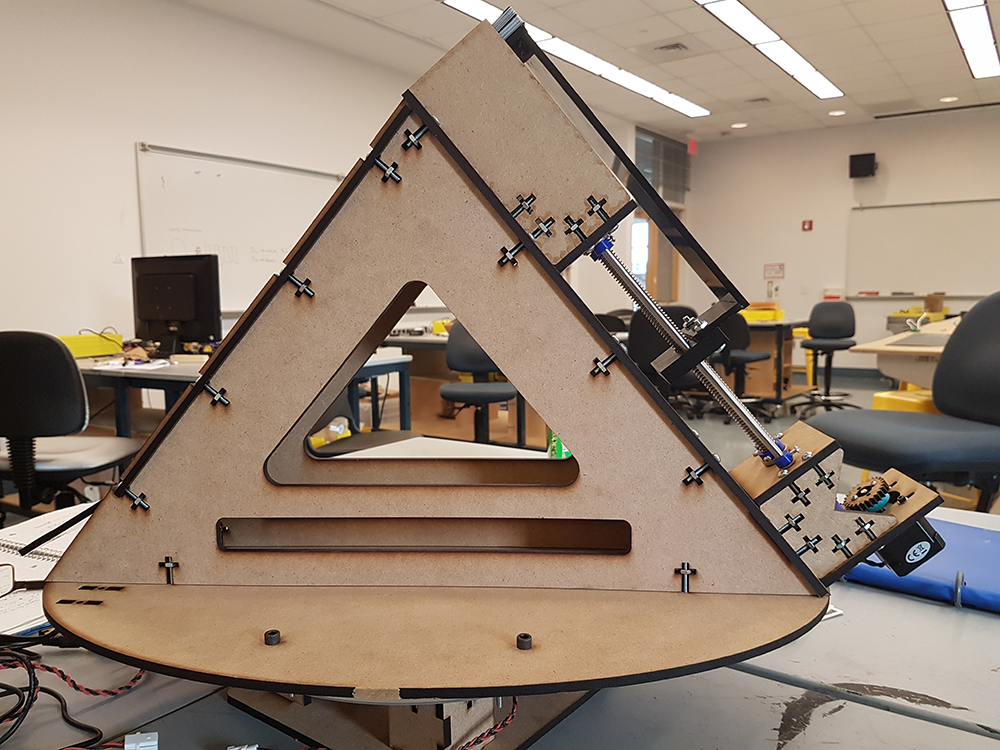
The mountain structure was first designed and fabricated in the second iteration and it was originally an isosceles triangle where the equivalent sides were 18 inches long, which made the height of just the mountain structure approximately 15 inches tall! On the other side of the mountain structure was a lasercut slide that was made in two pieces with finger joints and superglued together to create the angle. The slide was very effective in preventing the cards from flipping over so that element was carried forth into the following iterations. We also put in a large access hole in the triangular piece so that we could attach and detach the card advancer without disturbing the rest of the robot. The access hole was also very useful in wiring our system.
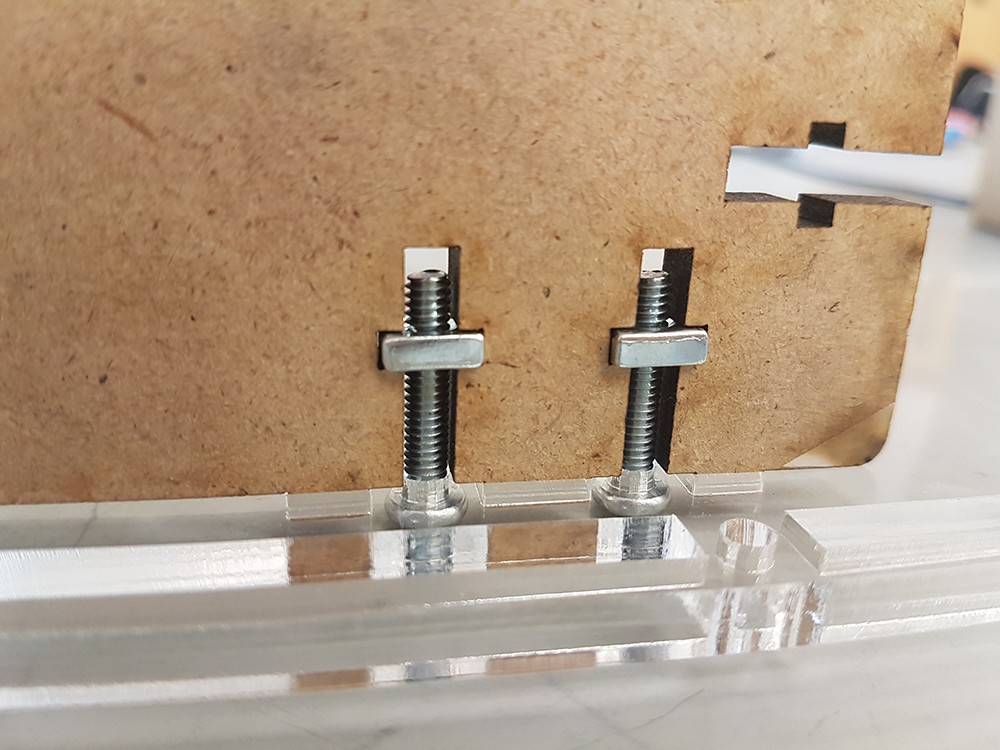
The mountain structure and parts of the card advancer were all held together with screw-reinforced mortise and tenon joints with our standardized 8-32 bolts and square nuts. This type of fastening was very effective at providing a strong hold and enabled easy assembly. The square nut slips into the slot of one piece and the bolt fits into the hole of the other. The slot holds the square nut rotationally in place so that you don't have to hold it and it acts as a locknut.
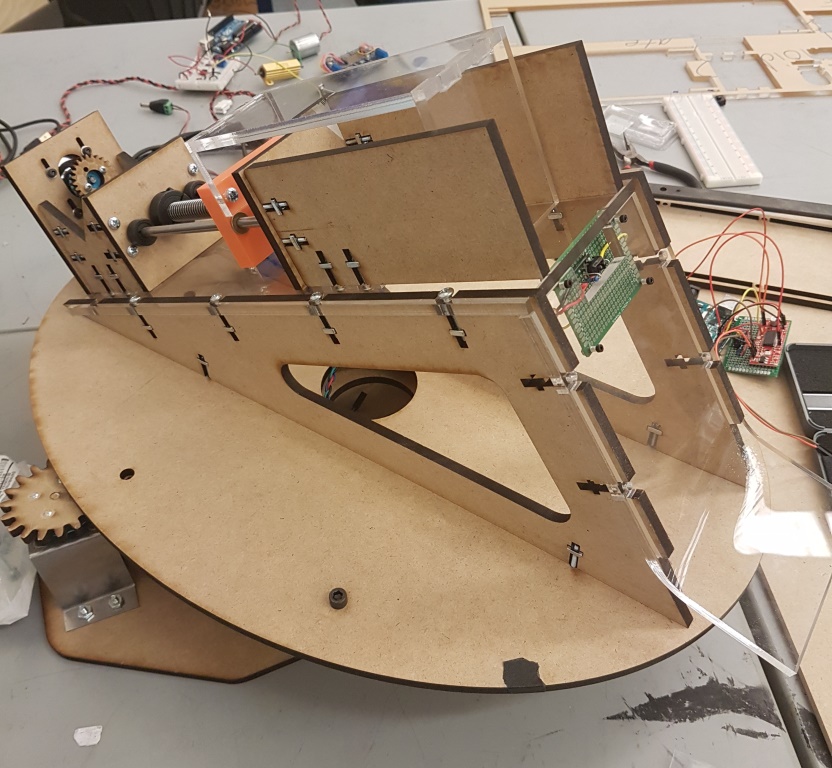
In the third iteration we focused on shortening the mountain structure vertically and horizontally while still being able to hold 6 decks of cards. We opted for a scalene triangle where the longer side was for the card advancer and the shorter side was for the slide. To make the slide we tried to heat-bend it to the angle that we desired. We use 1/4" acrylic so it took a few minutes of passing the heat gun over it, but once it softened it would bend quite easily. The only thing we had to watch out for was bubbles, they would start forming if the acrylic gets too hot and it affects the surface finish. After cooling the acrylic slide shrunk ever so slightly so it had some difficulty mounting onto the tenons of the triangles. So a few minutes of filing key spots made it fit right back in. On the top of the slide we added a notch for an IR reflectance sensor, which would detect if a card has been dealt so that we could deal a precise number of cards. After adding in the IR reflectance sensor we were able to consistently deal one card ~95% of the time.
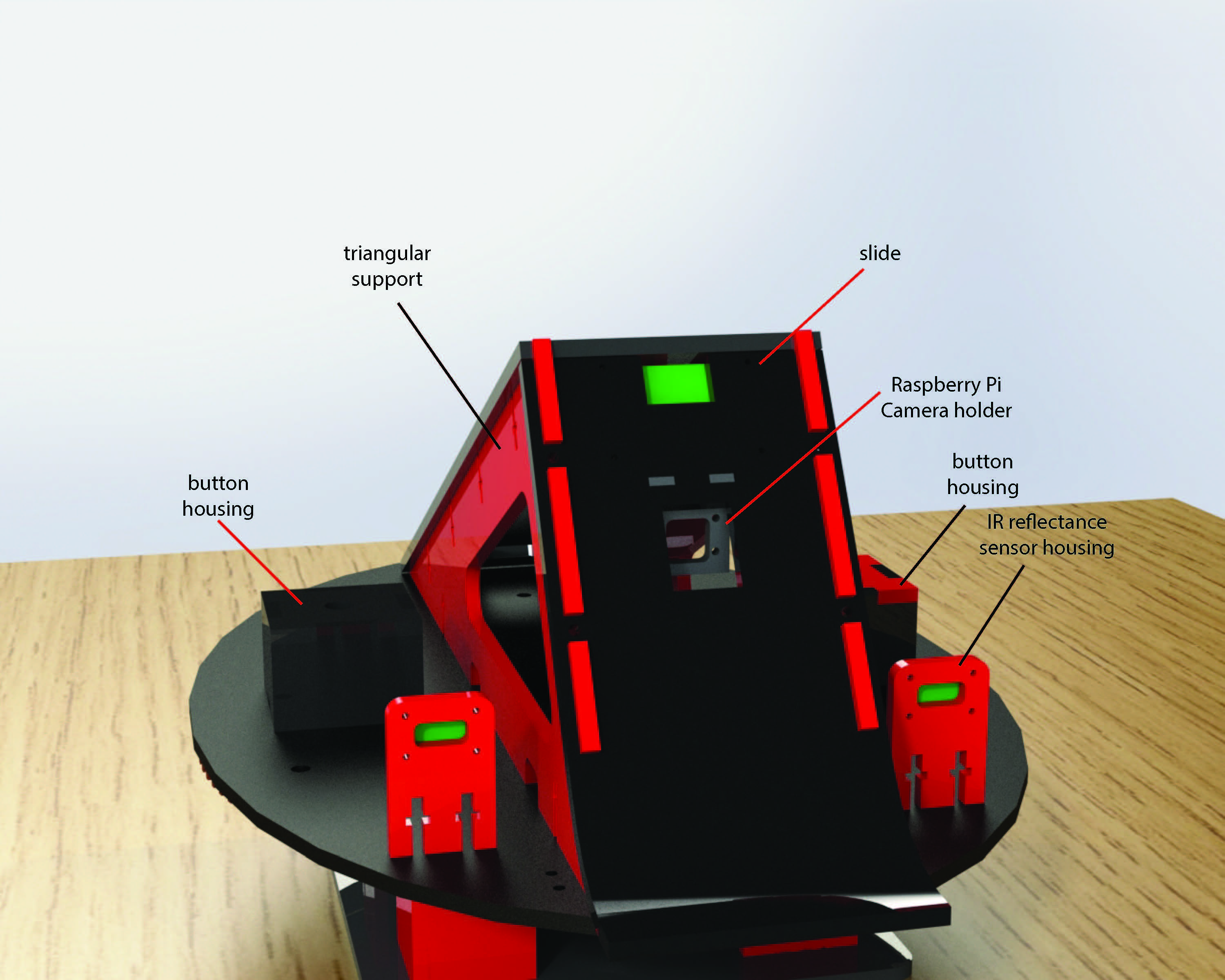
For the latest iteration the structure didn't change from the third iteration. We did add some notches on the bottom of the triangular pieces for wiring and holes in the slide to mount the fixture for the Raspberry Pi Camera. This time the slide was lasercut out of black acrylic to go with our aesthetic and heat-bent to obtain the angle. Aside from the mountain structure, we also added some button housings and IR reflectance sensor holders on either side of it for user inputs.
Things to keep in mind
- Design for modularity so that subsystems can be taken off and tested individually without interfering other components.
- When designing, keep in mind that the wires can't magically pass through your material unless you put holes in them
- Make sure that the MDF you are lasercutting is flat to avoid warped pieces
- Don't overheat acrylic if you are heat-bending, you will know if it starts to form little bubbles
- Use good fastening techniques (a.k.a. don't glue everything together)